Monday, April 4, 2011
Oak and Walnut Transformed Pt 2
Well after a delay longer than I planned I finally got to finish up my rod rack. Don’t know what I was waiting on since it only took about an hour to have it ready to put back together. Anyway here are the final few steps in our rod rack as furniture project.
I started with the idea to use scrap wood to do a budget build but my buddy over at http://www.funcfish.com/ beat me to it and did a great job so there was no need for me to do it again. This build used the same idea, materials already in the shop, yes I have a lot of stuff available, to create something nice enough to bring inside not leave in the garage. With the help of my neighbor’s shop and wood supply I was able to do this project for zero cost. All materials were leftovers from previous projects, wood rescued from various places or bulk buys from auctions at very low cost long since recouped.
Getting back into the shop I had to decide where to drill holes for rods to sit. I measured the top board from the end to find the exact middle then working toward each end, put a mark every 5 inches ending up with 7. There is no reason for putting them at this spacing other than it looked good. This spacing will allow me to add a series of holes on the other side if I want to add more rods. If I do I will offset the holes to provide more room for the reels on the lower shelf. I measured in from the edge 1 ½ inches and using a center punch made a small hole to guide a 1” forstner’s bit to drill each hole using a drill press. Be sure and drill from the top and put a board under your work piece to minimize tear out. By drilling from the top any tears will be hidden underneath. Next I cut a half inch slot for each hole using a square to guide my Japanese handsaw, you could use a jig saw or another type of handsaw but I have this one and it is great for cuts like this. This finished the top shelf except for a final sanding.
Drill press with Forstner's bit and backer board. Oh and a cluttered workbench.
The trim added to the top of each side piece needed shaping on each corner plus the walnut was too wide and had to be sanded to blend with the oak. I shaped the corners on my bench top belt/disc sander, I had considered a bunch of ways to layout the curve but in the end just eyeballed it. To cut down the extra width I used a palm sander with 60 grit paper to get it close then switched to100 grit. I used 220 grit paper for a final sanding and to round over any edges on all of the pieces. Everything was wiped down with a tack cloth to remove dust to get ready for stain.
Belt/disc sander and my Japanese saw. I love this saw it was sent from Tokyo by a friend.
To keep the contrast high between the two colors of wood I decided to use walnut stain on the trim pieces but just a natural stain on the oak. To do this I used a small cloth folded into a point to carefully apply stain to all trim pieces first. Take your time so you don’t get dark stain on the lighter oak. If you do lightly sand it using a small piece of 400 grit after the walnut stain dries so you don’t contaminate the trim pieces with dust. After the walnut is done I used a cloth to apply the natural stain to the oak. I like to use old t-shirts since they tend to be lint free and soft to keep the streaks down. This goes fast since I use a product that is stain and polyurethane in the same can.
End details with walnut pegs in mortises.
The last step is to cut some small pieces of cedar to hold the rods in place, just in case. You could use more walnut which would look good but I was lazy and used a piece of cedar already milled to the size I needed I found laying on a work bench. I had several ideas on how to keep the rods in place but this one was the fastest so it won out. Each cedar piece was finished with the natural stain and there we have it, finally finished. I realized as I loaded the pictures I left these out but you get the idea.
And finally the finished piece.
This is an old form of joinery which I have been fascinated with for years. The idea that simple friction will hold a piece of furniture together is just cool stuff. Yes it does take a bit of fitting but in the end you have no nails or screws to hide plus it can be taken apart if you have to move or ship it.
This rod rack can be built with nothing but a few hand tools and a bit of space to lay things out. I’m lucky to have access to tools, two shops and a large quantity of lumber but I have done things like this with much less. One bit of advice on lumber, if you look you might find a sawmill close that you never paid attention to. We make regular visits to several in our area and buy wood at a tiny fraction of what it would cost at a lumber yard or box store. It takes more work to get it ready to use but the savings are huge. Don and I just made three tables from wood saved from a burn pile at Trott’s Mill where a truck load cost us $10.00. Except for the attachments for the legs the cost was pennies for each one. These will sell in the $100.00 range for a total cost to us of under $5.00 each.
Hope you enjoyed a bit more woodworking, thanks for taking some time to check it out.
I started with the idea to use scrap wood to do a budget build but my buddy over at http://www.funcfish.com/ beat me to it and did a great job so there was no need for me to do it again. This build used the same idea, materials already in the shop, yes I have a lot of stuff available, to create something nice enough to bring inside not leave in the garage. With the help of my neighbor’s shop and wood supply I was able to do this project for zero cost. All materials were leftovers from previous projects, wood rescued from various places or bulk buys from auctions at very low cost long since recouped.
Getting back into the shop I had to decide where to drill holes for rods to sit. I measured the top board from the end to find the exact middle then working toward each end, put a mark every 5 inches ending up with 7. There is no reason for putting them at this spacing other than it looked good. This spacing will allow me to add a series of holes on the other side if I want to add more rods. If I do I will offset the holes to provide more room for the reels on the lower shelf. I measured in from the edge 1 ½ inches and using a center punch made a small hole to guide a 1” forstner’s bit to drill each hole using a drill press. Be sure and drill from the top and put a board under your work piece to minimize tear out. By drilling from the top any tears will be hidden underneath. Next I cut a half inch slot for each hole using a square to guide my Japanese handsaw, you could use a jig saw or another type of handsaw but I have this one and it is great for cuts like this. This finished the top shelf except for a final sanding.
Drill press with Forstner's bit and backer board. Oh and a cluttered workbench.
The trim added to the top of each side piece needed shaping on each corner plus the walnut was too wide and had to be sanded to blend with the oak. I shaped the corners on my bench top belt/disc sander, I had considered a bunch of ways to layout the curve but in the end just eyeballed it. To cut down the extra width I used a palm sander with 60 grit paper to get it close then switched to100 grit. I used 220 grit paper for a final sanding and to round over any edges on all of the pieces. Everything was wiped down with a tack cloth to remove dust to get ready for stain.
Belt/disc sander and my Japanese saw. I love this saw it was sent from Tokyo by a friend.
To keep the contrast high between the two colors of wood I decided to use walnut stain on the trim pieces but just a natural stain on the oak. To do this I used a small cloth folded into a point to carefully apply stain to all trim pieces first. Take your time so you don’t get dark stain on the lighter oak. If you do lightly sand it using a small piece of 400 grit after the walnut stain dries so you don’t contaminate the trim pieces with dust. After the walnut is done I used a cloth to apply the natural stain to the oak. I like to use old t-shirts since they tend to be lint free and soft to keep the streaks down. This goes fast since I use a product that is stain and polyurethane in the same can.
End details with walnut pegs in mortises.
The last step is to cut some small pieces of cedar to hold the rods in place, just in case. You could use more walnut which would look good but I was lazy and used a piece of cedar already milled to the size I needed I found laying on a work bench. I had several ideas on how to keep the rods in place but this one was the fastest so it won out. Each cedar piece was finished with the natural stain and there we have it, finally finished. I realized as I loaded the pictures I left these out but you get the idea.
And finally the finished piece.
This is an old form of joinery which I have been fascinated with for years. The idea that simple friction will hold a piece of furniture together is just cool stuff. Yes it does take a bit of fitting but in the end you have no nails or screws to hide plus it can be taken apart if you have to move or ship it.
This rod rack can be built with nothing but a few hand tools and a bit of space to lay things out. I’m lucky to have access to tools, two shops and a large quantity of lumber but I have done things like this with much less. One bit of advice on lumber, if you look you might find a sawmill close that you never paid attention to. We make regular visits to several in our area and buy wood at a tiny fraction of what it would cost at a lumber yard or box store. It takes more work to get it ready to use but the savings are huge. Don and I just made three tables from wood saved from a burn pile at Trott’s Mill where a truck load cost us $10.00. Except for the attachments for the legs the cost was pennies for each one. These will sell in the $100.00 range for a total cost to us of under $5.00 each.
Hope you enjoyed a bit more woodworking, thanks for taking some time to check it out.
Labels:
fishing,
rod rack,
woodworking
Subscribe to:
Post Comments (Atom)
About Me
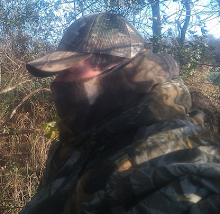
- Tommy Ellis
- Born and raised in middle Tennessee.I'm a working wildlife and landscape artist specializing in watercolors. Now making cedar lures and custom turkey calls.
Followers
Search
Powered by Blogger.
6 comments:
That's a very cool, elegant design there, Tommy. Something like that would make a great gift for my dad, who seems to already have everything!
Wow that rack is a vision! (of what I was really trying to do with mine) NICE JOB!
Very nice work.
Good dispatch and this enter helped me alot in my college assignement. Gratefulness you on your information.
aromatherapy
That looks great and what an awesome design! I love the fact that you can assemble and disassemble it with ease too.
Nicely done!
ok... now that's just plan gorgeous and so functional. need one for my office, especially for those lunch breaks to the state park nearby.
Post a Comment