Tuesday, February 1, 2011
Oak and Walnut Transformed
I got inspiration from my friend @funcfish on Twitter (look in the top right for a link to his site) and the fact that I had a pile of rods stacked in the corner. He did a budget rod rack that is very functional, so, I thought I would try to do one that is a bit fancier and more like furniture. The main reason is my rods are kept in my office/outdoors room and I wanted to see if I could make it nice enough to fit inside the house. This might not be a beginner’s project and while you can do it with hand tools, it is much easier with a room full of woodworking stuff.
Staying with his idea of using what was on hand, I headed to the wood shop after a little planning to see what was there. I picked out some antique oak that had been saved from an old barn. This stuff is hard as a rock and not a lot of fun to work with but there was enough of it and some boards needed to be used since they were cracking. There was some walnut laying there for a good contrast in color for the trim. You could use whatever you like to do this project, pine would be very easy to use. If you do use pine I would still use a hardwood for the pegs that hold things together. So, here we go.
The choices, oak, poplar, cedar, walnut
Parts list
2 pieces - 5” x 42” x ¾”
2 pieces - 5” x 30” x ¾”
2 pieces - 2” x 10” x ¾”
2 pieces - ¾” x ¾”
4 pieces - 2 ½” x 1”x 1”
Wood glue
There are no nails or screws needed for this project.
After picking out the boards they were run through the planer to true the sides and get them down to ¾ inch thickness. These were then cut to length and ripped to width on the table saw to true the ends and edges. In woodworking terms this is S4S or surfaced on 4 sides.
Don't try to take a pic while holding onto the board being planed.
Don ripping boards to width.
This project uses mortise and tenon joinery for the four main pieces and dowels for adding the feet. I laid out the tenons on the long boards. From the end measure back 3” and mark across the board. Then measure in from each side 1” and cut these pieces out leaving a tenon 3”x3”. I used a band saw but a jig saw would work or a hand saw if you take your time. For the mortise measure in 1” from each side of the tenon, from the end of the tenon measure back 1 ¼” and make a mark then another at 2 3/8”. This should give you a rectangle one inch by one and an eighth. Check to be sure the mortise is 5/8” from the back of the tenon it needs to be inside the vertical board, you will see why later. Repeat this on the ends of both long boards. You should have two boards measuring 42” with a 3” tenon on each end leaving a section in the middle measuring 36” from tenon to tenon.
Tenon cut on band saw. Note the mortise laid out on board.
The crappy mortiser.
This is what you end up with before trueing with files.
For the shorter end boards you need a mortise near each end for the long boards to fit into. On one end measure in down 1”and mark across the board then measure down another ¾” and make another mark. Measure in from each side 1”. This should give you a rectangle ¾”x 3”. On the other end measure down 2” and then repeat the rest of the step above. Once all of the mortises are laid out I used a dedicated mortiser to remove the material. You could do the same thing by drilling holes near the corners then use a jig saw (I wish I had) which would have worked better than the junky mortiser I used.
Once all of the mortise and tenons are cut I needed to true them and fit each part together. This is done with a set of woodworker’s files and rasps. Decide which side is up on the long boards and always test your fit with the same tenon going into the same mortise. I numbered mine and marked the top to be sure I didn’t mix them up. On the short boards the mortise that is 1” from the end is the bottom and will have the foot attached later.
Cleaning up the mortise with a file.
Top shelf being test fitted.
After fitting the pieces I picked the walnut I was using for trim. Instead of drilling shallow holes into the bottom to accept the rod handles I decided to add a raised piece of trim measuring ¾” x ¾” along the front and back edge of the bottom shelf. These were cut long, glued then clamped in place to dry. Be sure the edges line up as best as you can to cut down on sanding later. But if they are off a bit sanding blends them so don’t worry too much, just get them as close as you can. After they dry I cut the trim to length using a Japanese trim saw. While these are drying you can work on the sides, feet and trim for the top.
Prepping the walnut.
Clamped and waiting for glue to dry on walnut trim.
I made the pattern for the feet using a scrap piece of wood but you could use cardboard. I drew the pattern on the scrap, cut it close on the band saw then finished it on the oscillating drum sander. This was used to transfer the shape to the ends of the feet. Use double sided tape to hold the feet together then cut the excess away on the band saw. Using the oscillating sander I sanded down to the line making the feet match. These are attached to the end boards using wooden dowels. Find the center of the side piece and the center of the foot. Measure out from the center 1 ¾” toward the edge and drill a hole in the center of the board one size larger than the dowel. I used the bit to enlarge and taper the hole to give me some wiggle room in making them fit. Cut the dowels to length, add glue and attach the foot to the side. I used bar clamps to draw everything together. Again try to get things as even as you can to cut down on sanding.
I wanted a piece of walnut trim on the top of the ends to give them a finished look. I cut two pieces of walnut 5 ¼” long x ¾” square. I glued these to the tops, clamping them with bar clamps till dry. After they were dried I drew a radius on the top corners and I will sand to the line, giving them a nice curve instead of sharp corners.
To hold everything together you need 4 wedges, which I made out of a scrap of walnut. I cut them into 1” squares 2 ½” long then shaped them on the belt/disc sander. You need to add a taper to one side so that as it tightens it will push everything together. Take your time and test fit these frequently to be sure you get a good fit and don’t take off too much material. This piece really needs to be made from hardwood even if you chose to work with pine for the rest of the boards.
Cutting the wedges on the band saw.
Testing the wedges. Look close on top of wedge you will see it is numbered.
I was planning to finish this in one post but things got in the way. Here is a shot of the almost finished piece. I still need to drill holes for the rods, cut slots back to the holes, make walnut pegs to hold rods in place, finish sanding and add finish. This sounds like a lot but it really isn’t but other things have kept me from getting it done. I will get it finished up in a few days and post the last few steps and pictures of the finished piece.
Staying with his idea of using what was on hand, I headed to the wood shop after a little planning to see what was there. I picked out some antique oak that had been saved from an old barn. This stuff is hard as a rock and not a lot of fun to work with but there was enough of it and some boards needed to be used since they were cracking. There was some walnut laying there for a good contrast in color for the trim. You could use whatever you like to do this project, pine would be very easy to use. If you do use pine I would still use a hardwood for the pegs that hold things together. So, here we go.
The choices, oak, poplar, cedar, walnut
Parts list
2 pieces - 5” x 42” x ¾”
2 pieces - 5” x 30” x ¾”
2 pieces - 2” x 10” x ¾”
2 pieces - ¾” x ¾”
4 pieces - 2 ½” x 1”x 1”
Wood glue
There are no nails or screws needed for this project.
After picking out the boards they were run through the planer to true the sides and get them down to ¾ inch thickness. These were then cut to length and ripped to width on the table saw to true the ends and edges. In woodworking terms this is S4S or surfaced on 4 sides.
Don't try to take a pic while holding onto the board being planed.
Don ripping boards to width.
This project uses mortise and tenon joinery for the four main pieces and dowels for adding the feet. I laid out the tenons on the long boards. From the end measure back 3” and mark across the board. Then measure in from each side 1” and cut these pieces out leaving a tenon 3”x3”. I used a band saw but a jig saw would work or a hand saw if you take your time. For the mortise measure in 1” from each side of the tenon, from the end of the tenon measure back 1 ¼” and make a mark then another at 2 3/8”. This should give you a rectangle one inch by one and an eighth. Check to be sure the mortise is 5/8” from the back of the tenon it needs to be inside the vertical board, you will see why later. Repeat this on the ends of both long boards. You should have two boards measuring 42” with a 3” tenon on each end leaving a section in the middle measuring 36” from tenon to tenon.
Tenon cut on band saw. Note the mortise laid out on board.
The crappy mortiser.
This is what you end up with before trueing with files.
For the shorter end boards you need a mortise near each end for the long boards to fit into. On one end measure in down 1”and mark across the board then measure down another ¾” and make another mark. Measure in from each side 1”. This should give you a rectangle ¾”x 3”. On the other end measure down 2” and then repeat the rest of the step above. Once all of the mortises are laid out I used a dedicated mortiser to remove the material. You could do the same thing by drilling holes near the corners then use a jig saw (I wish I had) which would have worked better than the junky mortiser I used.
Once all of the mortise and tenons are cut I needed to true them and fit each part together. This is done with a set of woodworker’s files and rasps. Decide which side is up on the long boards and always test your fit with the same tenon going into the same mortise. I numbered mine and marked the top to be sure I didn’t mix them up. On the short boards the mortise that is 1” from the end is the bottom and will have the foot attached later.
Cleaning up the mortise with a file.
Top shelf being test fitted.
After fitting the pieces I picked the walnut I was using for trim. Instead of drilling shallow holes into the bottom to accept the rod handles I decided to add a raised piece of trim measuring ¾” x ¾” along the front and back edge of the bottom shelf. These were cut long, glued then clamped in place to dry. Be sure the edges line up as best as you can to cut down on sanding later. But if they are off a bit sanding blends them so don’t worry too much, just get them as close as you can. After they dry I cut the trim to length using a Japanese trim saw. While these are drying you can work on the sides, feet and trim for the top.
Prepping the walnut.
Clamped and waiting for glue to dry on walnut trim.
I made the pattern for the feet using a scrap piece of wood but you could use cardboard. I drew the pattern on the scrap, cut it close on the band saw then finished it on the oscillating drum sander. This was used to transfer the shape to the ends of the feet. Use double sided tape to hold the feet together then cut the excess away on the band saw. Using the oscillating sander I sanded down to the line making the feet match. These are attached to the end boards using wooden dowels. Find the center of the side piece and the center of the foot. Measure out from the center 1 ¾” toward the edge and drill a hole in the center of the board one size larger than the dowel. I used the bit to enlarge and taper the hole to give me some wiggle room in making them fit. Cut the dowels to length, add glue and attach the foot to the side. I used bar clamps to draw everything together. Again try to get things as even as you can to cut down on sanding.
I wanted a piece of walnut trim on the top of the ends to give them a finished look. I cut two pieces of walnut 5 ¼” long x ¾” square. I glued these to the tops, clamping them with bar clamps till dry. After they were dried I drew a radius on the top corners and I will sand to the line, giving them a nice curve instead of sharp corners.
To hold everything together you need 4 wedges, which I made out of a scrap of walnut. I cut them into 1” squares 2 ½” long then shaped them on the belt/disc sander. You need to add a taper to one side so that as it tightens it will push everything together. Take your time and test fit these frequently to be sure you get a good fit and don’t take off too much material. This piece really needs to be made from hardwood even if you chose to work with pine for the rest of the boards.
Cutting the wedges on the band saw.
Testing the wedges. Look close on top of wedge you will see it is numbered.
I was planning to finish this in one post but things got in the way. Here is a shot of the almost finished piece. I still need to drill holes for the rods, cut slots back to the holes, make walnut pegs to hold rods in place, finish sanding and add finish. This sounds like a lot but it really isn’t but other things have kept me from getting it done. I will get it finished up in a few days and post the last few steps and pictures of the finished piece.
Subscribe to:
Post Comments (Atom)
About Me
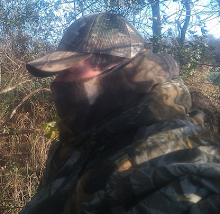
- Tommy Ellis
- Born and raised in middle Tennessee.I'm a working wildlife and landscape artist specializing in watercolors. Now making cedar lures and custom turkey calls.
Followers
Search
Powered by Blogger.
4 comments:
Nice shop! I'm jealous...
Yep a 40 x 50 foot woodworking and metal working playground. It belongs to my neighbor, Don.
That's some real fine lookin' work there! Wish I was talented enough to do stuff like that but I'd more than likely loose a finger... or two!
Very cool, Tom. I am definitely looking forward to seeing the final piece. Who knows, you may inspire me to start using the wood I have saved up.
Post a Comment